Metal Stamping is a general term that describes many kinds of fabricating processes to shape metal. Those metal processing techniques range from blanking, bending, punching, piercing and others to shape metal into functional components. The production machines to process these parts range from very simple metal stamping machines to automated metal stamping systems.
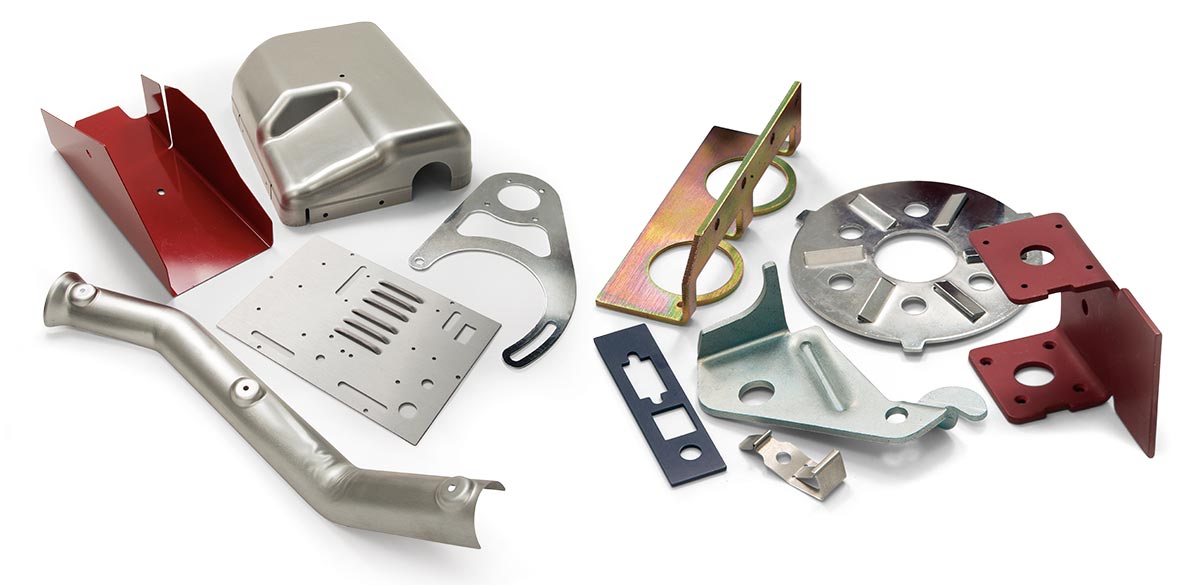
Quantities of metal stamped parts can range from just a few hundred components to many thousands, or hundred of thousands. These parts are used in:
- Snowmobiles
- Office furniture and equipment
- Electrical equipment
- Medical Equipment
- Automotive Assemblies
- Aircraft
- And Many Other Manufactured Products
Four factors determine which metal stamping process is ideal for the shaped metal application:
- Cost
- Quantity
- Quality
- Time to manufacture
The material required for the application also affects the selection of the metal shaping process. The range of available metals is very large.
Metal Stamping Considerations:
Tool die design is critical for determining all part features including:
- Component shape
- Part edges
- Tolerances desired
- Overall part quality.
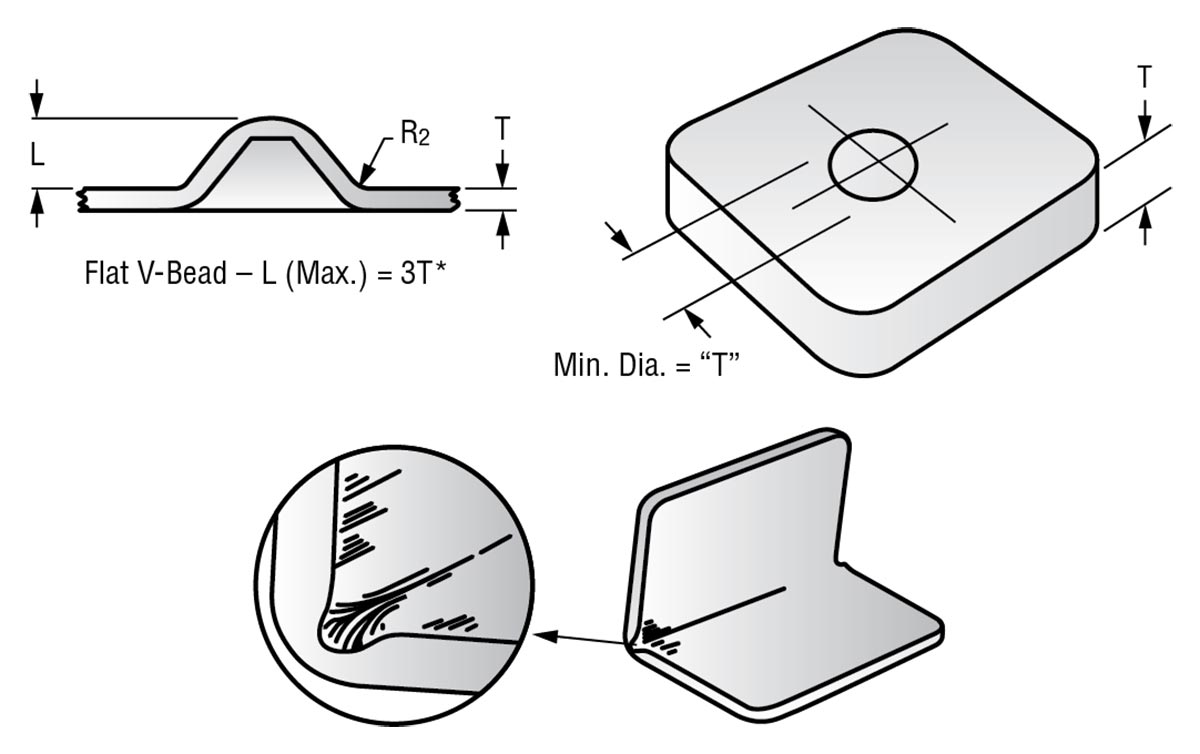
Primary Metal Stamping Processes
The two most common metal stamping processes, used to manufacture a wide variety of components, are Short Run Stamping and Progressive Die Stamping.
Short-Run Stamping: Fast and Cost Effective
Short-run metal stamping is a process used to manufacture smaller quantities of punched parts. A short run application is typically:
- Less than 5,000 parts.
- Simple in Shape & Size
- Made of basic materials eg. cold rolled steel, aluminum and similar materials.
These types of parts are stamped on basic open back inclinable (OBI) punch presses and straight side automatic presses that are fast to setup and operate.
The short run stamping process is ideal for:
- Prototype Production Runs
- Replacement Parts
- Short Life Products
- Modified Products
- And Similar Applications
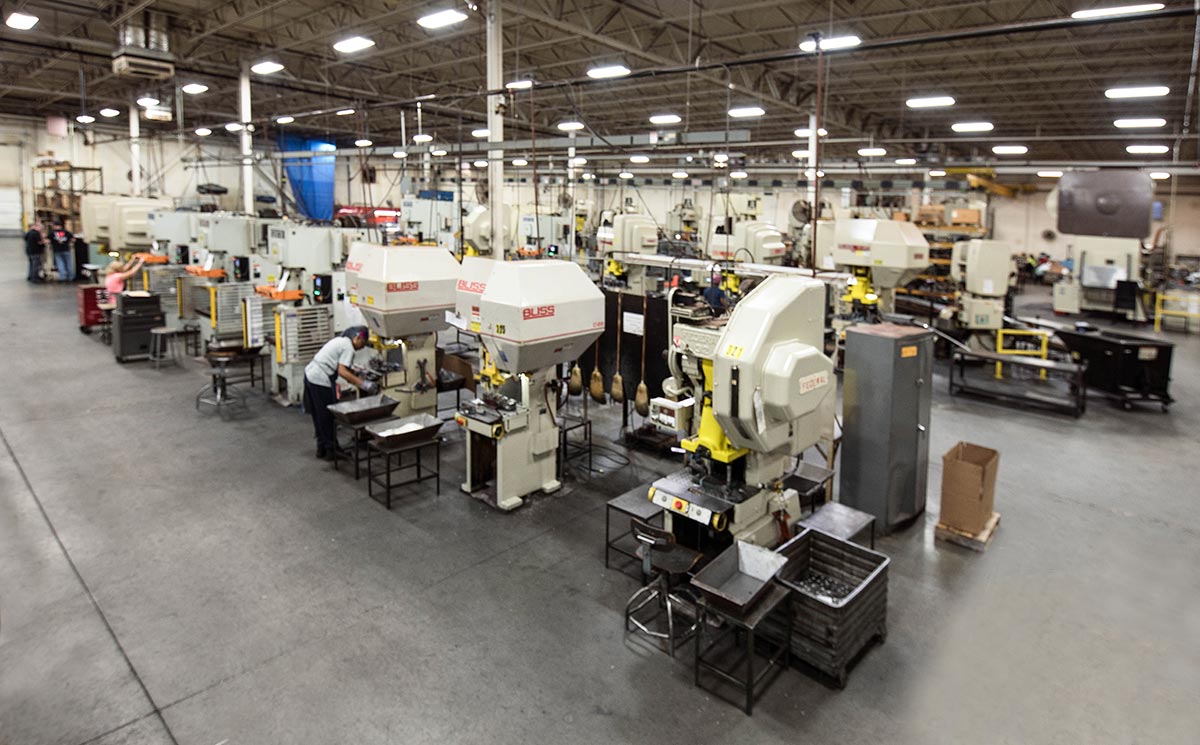
Progressive Die Stamping: Large Quantities & Complex Parts
Progressive die stamping utilizes a press with an automatic feeding system to advance a strip of metal, unrolled from a coil, through a series of stamping stations. As the material is punched and advanced, a web of material results which continues the series of punching operations. The completed parts fall away from the scrap web material into large containers as the punching process continues uninterrupted.
The progressive stamping method can modify raw material into a completed component by:
- Punching
- Coining
- Bending
- Drawing
- Trimming
- And more
Key to the progressive stamping method is the die, which is designed with a series of punching stations that advance the part forming sequence to completion. The progressive stamping die is placed into a reciprocating stamping press. These presses can:
- Fabricate Larger Parts
- Incorporate Automation
- Produce longer Part Runs
- Operate At Higher Speed
Tooling dies for progressive stamping require sophisticated CAD/CAM design and manufacture. Considered permanent tooling, lead time requirements are far greater compared to short run tooling setups. Progressive tooling costs are significant and need to be amortized over a long production run of 10,000 and more components.
Progressive die metal stamping is ideal for long product life cycle part applications used in automotive, off-highway vehicles, aircraft, and similar product applications.
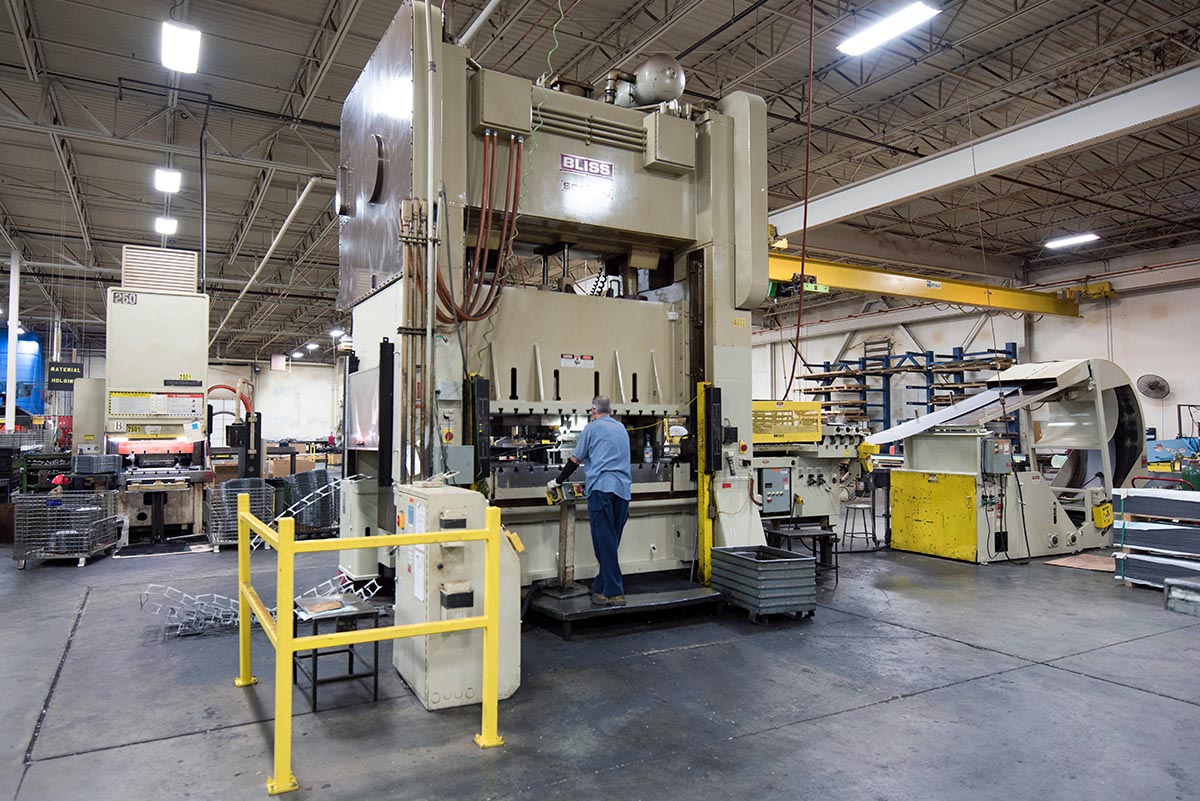
Additional Metal Stamping Methods
Multi-slide or Fourslide stamping forms metal coils into intricate shapes with multiple curves and bend radii greater that 90°. Multi-slide presses use a combination of laterally moving slides to form the component, unlike the conventional power presses described above. This process performs several operations almost simultaneously enabling forming the workpiece start to finish. Tooling flexibility for this process allows for easier future tooling modifications.
This is advantageous for certain parts requiring:
- Less Handling
- Fewer Machines
- Fewer Secondary Operations
Deep Drawn Stamping is a process of forming sheet metal under compressive and tensile conditions into a die. It produces a cavity with a closed bottom, and a round or irregularly shaped cup or cylinder. These are typically very long part runs. Examples are: Baking Pans, Aluminum Cans, etc.
Coining is a less common metal working process. It is a closed die forging process where pressure is applied on the surface of the forging. It creates close tolerances, smooth surfaces, and eliminates draft. This is predominantly a cold work process originally developed to produce coins.
Secondary Operations
All metal stamping methods may require secondary operations to successfully complete a satisfactory part for its intended application. These operations can include:
- Deburring
- Polishing
- Metal Finishing
- Painting